フリーベットブラックジャック
<ウェブサイト名>
<現在の時刻>
銅加工事業 電子材料事業 加工事業 金属事業 セメント事業 環境・エネルギー事業 アルミ事業 関連事業 ものづくり・R&D ホーム 事業 ものづくり・R&D 開発ストーリー 薄型テレビ自動分解技術 薄型テレビ自動分解技術 画像トラッキング技術で薄型テレビの高速自動化分解への挑戦 確実に訪れる、薄型テレビのリサイクル需要の大きな波。数年後を見据えて、人の手で行っていたねじ外し作業を確実・迅速に行なうため、「薄型テレビ自動分解システム」の開発に挑戦したメンバーに話を聞きました。 写真左より:多田(中央研究所)、後藤(東日本リサイクル)、瀬賀(環境リサイクル事業部) 「地デジ化」が話題となった2011年頃、ブラウン管テレビを薄型テレビに買い替えた思い出のある人も多いのではないでしょうか。テレビなどの家電については、家電リサイクル法により、家電メーカーの責任でリサイクルを進めることが義務付けられています。 一般家庭や事務所から排出された廃家電の、有用な部分や材料をリサイクルし、廃棄物を減量して資源の有効利用を推進しているのが、東日本リサイクルシステムズ&#12849;などのリサイクルプラントです。 全国的に薄型テレビの需要が一気に伸びたこの時期、環境リサイクル事業部では中央研究所と共同で、薄型テレビのリサイクル需要の高まりを見据えて「薄型テレビ分解システム」の開発が進められていました。 ベルトコンベヤーに載せられた薄型テレビのねじの位置を把握し、必要に応じて自動的に速度を調整するシステムと、その情報をもとにロボットが迅速・確実にねじを外していく技術を来る時代に先駆けて実用化しています。 将来の需要を見据えて、いま開発しなければ ──薄型テレビ分解システムの開発の経緯を教えて下さい。 多田 薄型テレビの売り上げが大幅に伸びた2011年頃、数年後にリサイクル需要の大きな波が来ることは容易に予測できました。効率的にリサイクルを進めるため、画像解析技術を活用して、手動で行っていたねじ外しを自動化できないかと考えたのが、薄型テレビ分解システム開発のきっかけです。 瀬賀 リサイクル需要の高まりは、薄型テレビのバックライトの寿命が切れる7〜8年後だと予想されていました。廃棄された大量の薄型テレビが当社に持ち込まれた時、一台当たり100〜250個にもなるねじを、手作業で外していてはとても対応しきれません。今こそ開発に着手しなくては、と試作機の開発に取りかかりました。 テレビの背面カバーを外し中のプリント基板のねじを外す ──開発にあたって、どんなことを行ったのでしょうか? 多田 まず行ったのは、ねじの形状や取り付け位置の調査・分析です。薄型テレビを手作業で分解し、使用されているねじを色味や形状、取り付け位置などのタイプ別に1本1本分類しました。ねじの量は多いもので1台300本ほど。上から取り付けられていることが多いのですが、横や下、パネルの裏に取り付けられているものもありました。また、それぞれのねじに、どんなタイプのドライバーが合うのか、外す際に回す力がどれくらい必要か、地道に調べ上げました。このデータをもとに実験と検証を繰り返した結果、6カ月後に試作機が完成。工場でまずデモンストレーションを行いました。 ねじだけを的確に見つける ねじ外し装置の動きをチェック ──試作機でのねじ外しは、いかがでしたか? 多田 デモンストレーション中はプレッシャーに押しつぶされそうでしたが、ドライバーが正確にねじを捉え、回転してねじを外した瞬間は、本当にホッとしました。 この試作機をベースに改良を重ね、1号機が完成したのです。 後藤 テレビの内部には、ねじ以外にもキラキラと光る部品がたくさんあり、ねじの位置を正確に判別するのは難しいのですが、試作機は次々とねじを見つけ、外していきました。その画像処理技術の高さ、ねじ外しの精度を披露できた瞬間でした。 ねじ外しのスピードアップに挑戦 手動でねじ外し作業を行なう様子 ──実用化に向けて、どんな課題があったのでしょうか。 後藤 新たに生じたのは、作業スピードの問題でした。ねじ外しを手動で行った場合、かかる時間は1個当たり約1.5秒。熟練した作業者はどこにねじがあるのか感覚的に分かるので、1個当たり1秒で取り外します。しかし1号機は、1個のねじを外すのに7秒もかかっていました。 瀬賀 しかし、現場では、作業者の入れ替わりや作業習得のために時間的なロスが発生しています。機械なら、安定したクオリティとスピードで、ムラなく一定のペースで作業することができるので、薄型テレビ分解システムが完成すれば、作業効率の向上や作業者の負担低減など、大きなメリットがあります。 ──薄型テレビ分解システムのスピードアップは、どのようにして実現したのでしょうか。 多田 冷蔵庫のリサイクル工程を見たことでアイデアが浮かびました。冷蔵庫を解体する時には、コンベヤーに載せてゆっくりと移動させながら作業を進めます。1号機は、カメラの画像を解析した後にねじを取り外していましたが、その工程を同時に行えば時間を短縮できるのではないかと考えました。 つまり、ベルトコンベヤーの上でテレビを移動させながら、画像処理でねじの位置を特定し、ねじ外しを行えば、時間短縮が可能になる訳です。 瀬賀 試行錯誤のうえ最終的に次のような装置システムを実現できました。 ねじの検出はベルトコンベヤーに載せられた直後に撮像エリアで行われます。薄型テレビは止まることなく動き続け、撮像エリアにある複数のカメラでねじの位置を検出します。 ベルトコンベヤーの速度は取り外すねじの数によって最適な速度を自動的に決定します。 撮像エリアで検出したねじの位置情報は分解エリアのロボットに伝達され、ロボットは素早く最適な位置に移動し、専用設計の電動ドライバーユニットで素早くねじを取り外します。 自動ねじ外し装置のイメージ図 各ユニットと制御信号のイメージ 多田 このような高度な仕組みによってテレビが動いたままでも確実に多くのねじを外すことができました。 後藤 しかし、コンベヤーで移動しながらねじ外しを行なうこの方式では、カメラが捉えたねじの位置が少しずつずれてしまうという問題がありました。これを解決するには、ベルトの蛇行を抑え、ねじとドライバーの位置を正確に合わせる必要があります。許されるズレは0.5mm以下。協力会社からもアイデアをいただき、試行錯誤を繰り返して、コンベヤーをスラットタイプに進化させた2号機が完成しました。 夜間に無人で解体を可能に ──実際に導入された薄型テレビ分解システムを使ってみて、いかがですか? 後藤 薄型テレビ分解システムの改良がどんどん進み、実際に使ってみると、「人の手の方が速いのではないか」という考えが全くなくなりました。今では、この装置のない現場は考えられないですね。稼働時間が長いこともメリットの一つです。人間は休まなければいけませんが、機械なら24時間稼働させても問題ありません。 多田 東日本リサイクルシステムズ&#12849;では現在、2台の薄型テレビ分解システムが日々安定的に稼働し、作業負担を軽減しています。 プリント基板上のねじを外すドライバー部 ──今後の展望についてお聞かせください。 多田 現状、薄型テレビ分解システムで取り外せるねじは背面カバーのねじで80%、プリント基板のねじで90%以上ですが、さらに精度を高め、できる限り100%に近づけたいです。 瀬賀 この装置のノウハウを家電リサイクルだけでなく、自動車リサイクルなど他のリサイクル業界へも発展していきたいと考えています。さまざまな会社で使用してもらい、フィードバックをいただいて、さらなる開発を進めてどんどん製品のクオリティを高めていければと思います。 開発ストーリー 開く 一覧へ 主な関係会社 開く 東日本リサイクルシステムズ株式会社 関連ウェブサイト 開く プレスリリース このページの先頭へ戻る ご利用にあたって 個人情報について 特定個人情報について サイトマップ 用語集 電子公告 © 2021 Mitsubishi Materials Corporation 当サイトでは利便性向上およびマーケティング活動のために閲覧履歴(クッキー)を収集しています。サイトご利用にあたっては右のボタンよりご同意お願いいたします。 なお、この設定の変更は「ご利用にあたって」の「閲覧履歴の収集」から行えます。 同意して閉じる
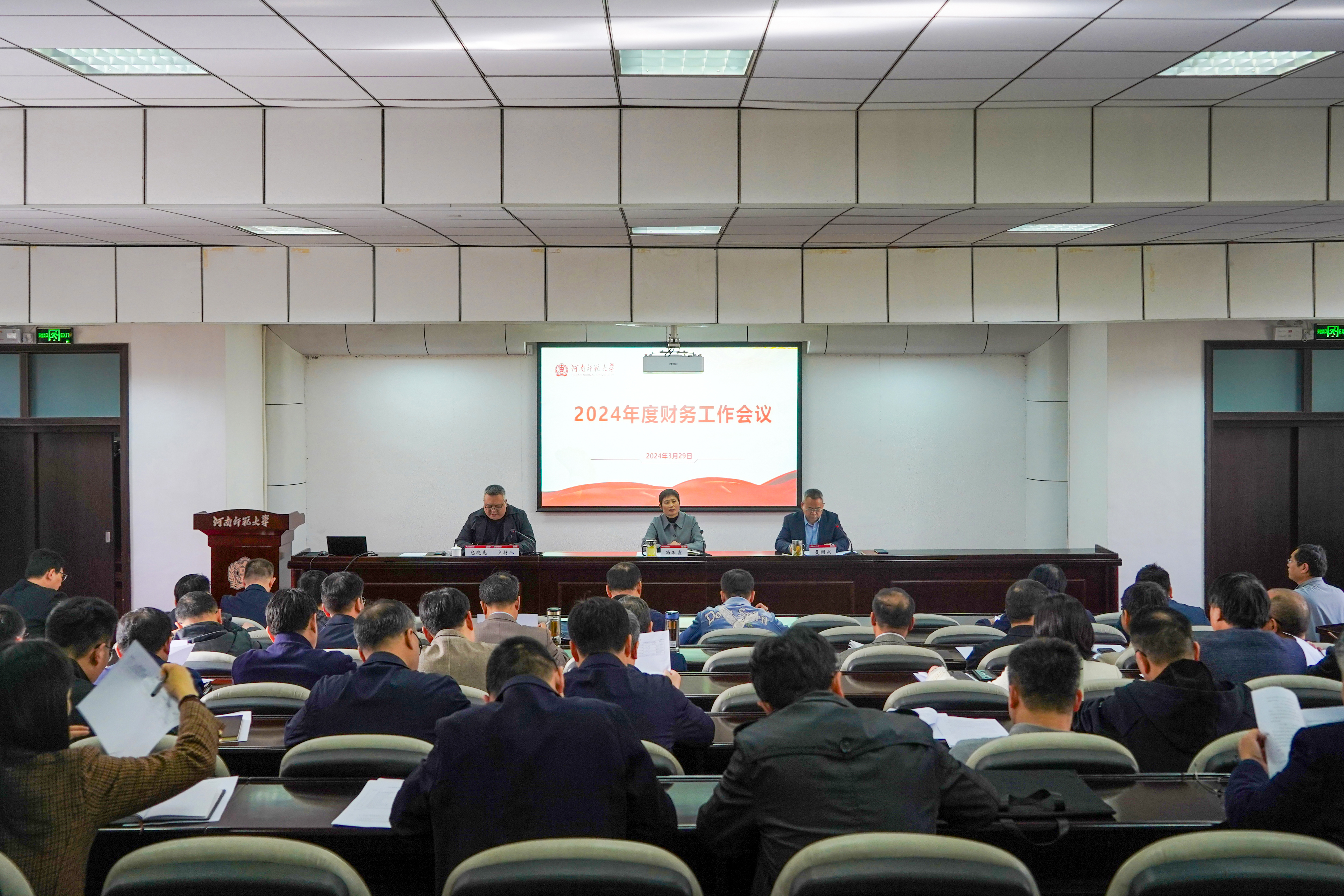